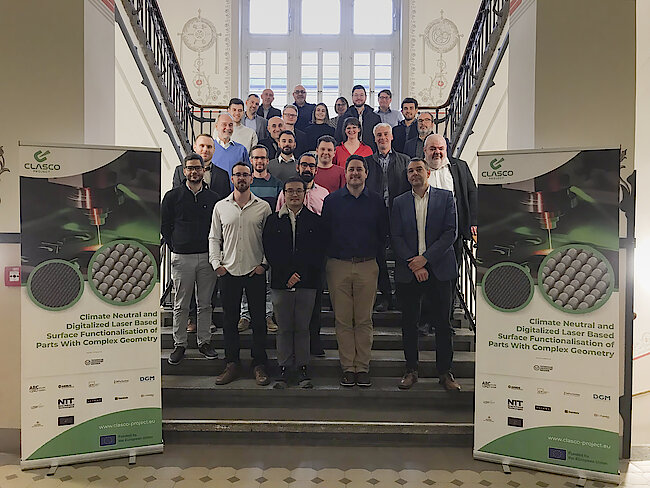
CLASCO-project meeting, 18 April 2023, TU Dresden
Project logo
European industry is facing the challenge of implementing carbon-neutral value chains in the future and producing sustainable products in order to remain competitive and meet climate change targets. In this context, innovative manufacturing processes are becoming increasingly important, such as fully digitalized 3D manufacturing. However, more complex components often require subsequent surface treatments, which in turn add to the cost and have an impact on the environment. CLASCO - Climate Neutral and Digitized Laser Based Surface Functionalisation of Parts with Complex Geometry - aims to replace these processes with digitized laser treatments. The project is funded by the EU's Horizon programme and Innovate UK with a total budget of around 5 million Euros. It will run from 1 January 2023 to the end of June 2026.
The innovative idea behind the CLASCO-project is explained by project leader Dr. Andrés Fabián Lasagni, Professor of Laser-Based Manufacturing at the Centre for Advanced Micro-Photonics (CAMP) at the Dresden University of Technology, explains: "The EU funding will allow us to develop a unique machine that can polish parts produced by additive manufacturing and create sophisticated surface features to increase the added value of the products. In addition, for the first time, various in-line monitoring methods will be used during the process. These include plasma sensors and infrared cameras. A virtual representation of the process will thus be possible for each part (digital twin), resulting in a fully digital product. The combination of laser polishing and laser micro structuring of the surface using Direct Laser Interference Patterning in one manufacturing system is a new method that will make production processes more sustainable in the future and enable carbon-neutral value chains. A consortium of 13 partner institutions from six European countries, including Spain, France, Ireland, the UK, Austria, and Germany, are working on the six project objectives in an interdisciplinary exchange.
The project partners are embedded in eight work packages. These focus on the sustainability of the laser-based process, inline process monitoring and the planned application-oriented implementation of the project results in the industry, in addition to the technological aspects.
The Deutsche Gesellschaft für Materialkunde e.V. (DGM), represented by Managing Director Dr. Stefan Klein and project member Dipl.-Ing. Sebastian Slawik is working together with Steinbeis, a global network and partner for knowledge and technology transfer, in the work package "Communication, Dissemination and Exploitation". The collaboration aims at broad public communication of the overall project, dissemination of project results in the scientific and industrial environment, and exploitation of key results for developing new and sustainable business models in the field of additive manufacturing. Through the organization of hybrid conferences, seminars, and workshops, the DGM will provide a platform for the networking of external and internal partners and thus increase the visibility of the project.
We present the project leader Prof. Dr. Andrés Fabián Lasagni in an interview and the use case partners in the news on the DGM homepage. All news about the CLASCO-project can be found on the project homepage and its social media channels, LinkedIn and Twitter.